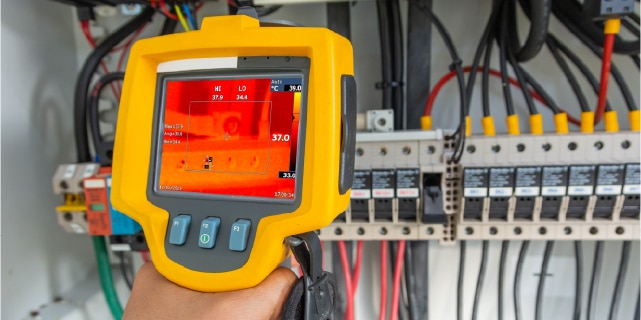
An often forgotten utility
Electrical distribution can often go forgotten, leading to lax or inconsistent maintenance and inspection. When electrical equipment fails it often leads to high equipment replacement costs, lengthy downtimes, and interruption in production or operations. One form of maintenance that can provide a huge benefit, with limited interruption in operation, is infrared thermography.
Infrared thermography
Often referred to as an infrared scan, infrared thermography utilizes special cameras to detect heat that cannot be seen by the human eye. This heat is typically produced through an increase in resistance in electrical equipment. Increased temperatures indicate a potential trouble spot that could lead to failure of the component and/or arcing. This can result in a shutdown in operations and personnel injury.
Because of this consideration, both the International Electrical Testing Association (NETA) and the National Fire Prevention Association (NFPA) recommend periodic infrared testing of critical equipment.
Benefits of a thermographic predictive maintenance program include:
- Minimized failures. Thermographic surveys help minimize maintenance cost and unscheduled outages.
- Increased safety. Detection of hot spots could prevent fire or arcing events.
- Minimal production interruption. Infrared thermography has to be completed when the equipment is at load; therefore, the maintenance activity will have minimal impact on production.
Infrared thermography can expand beyond electrical inspections to mechanical equipment. This is due to heat being generated when friction exists, or a lack of cooling medium being present. This allows the camera to see misalignment, bearing issues, clogged or obstructed cooling, and several other conditions which result in elevated heat.
What to expect with an infrared scan
Infrared scans do require some preparation and certain expectations should be made regarding a finished product. This will vary depending on the company completing the scan, as well as where the scan is completed.
The following items should be noted in preparation of a scan:
- Equipment should be under normal load.
- Plan the inspection route prior to the visit.
- Panels will need to be removed. Qualified personnel with proper PPE, training, and qualification should be made available.
What to expect once the infrared scan is completed:
- A completed report meeting NETA standards
- Complete list of items scanned
- Clear and concise description of the fault or issue noted, and recommendation
- Documentation of completed repair
- When to perform scans
Infrared scans should be completed periodically. This will be determined by equipment criticality, occupancy, environment, and exposure.
For occupancies dealing with heavy dust or dirt buildup or those that are part of heavy manufacturing, industry standard recommends annual inspection. For lighter occupancies such as high-rise buildings or light manufacturing facilities, the frequency will range between 2-3 years.
If findings are significant the frequency should be adjusted accordingly.
Visit our Equipment Breakdown page to learn more about protection for essential systems and equipment.
Featured insights
This website is general in nature, and is provided as a courtesy to you. Information is accurate to the best of Liberty Mutual’s knowledge, but companies and individuals should not rely on it to prevent and mitigate all risks as an explanation of coverage or benefits under an insurance policy. Consult your professional advisor regarding your particular facts and circumstance. By citing external authorities or linking to other websites, Liberty Mutual is not endorsing them.