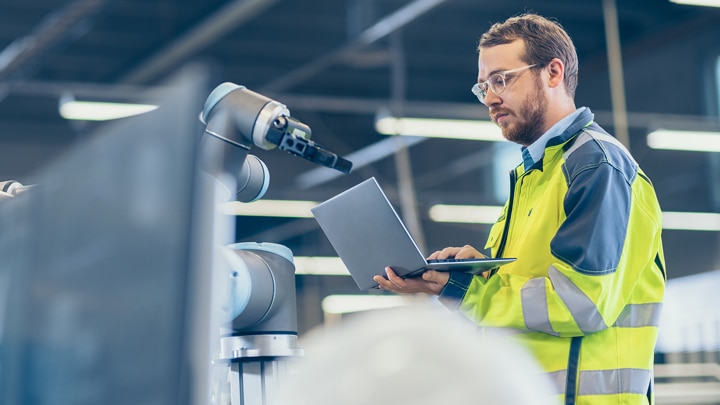
COVID-19 has put a strain on the manufacturing industry across the globe, as supply chain limitations and new health and safety regulations increase risk and threaten output. In fact, according to a recent report by Hitachi Vantara, three key challenges manufacturers struggle to manage as the pandemic continues include worker health and safety (74 percent of respondents rated a 3 or more on a scale of 1-5), productivity (66 percent), and supply chain disruption (65 percent).
As manufacturers look to address these challenges while managing costs, one solution shows significant promise: automation.
The effective deployment of automation equipment and processes can fundamentally change your business – and potentially reduce employee exposure to leading causes of workplace injury. In this article, we’ll review key reasons why the manufacturing industry is shifting to automation and three practices on how to incorporate it into operations for maximum impact.
Automation can increase productivity.
Even before COVID-19, manufacturers were looking for solutions to increase productivity despite significant reductions in the labor force.
According to FRED economic research, data indexed against 1990 benchmarks show that output has grown 44.2 percent in U.S. factories despite a 32.2 percent reduction in employment over the last 30 years. That means that the United States is producing 44 percent more goods than it did 30 years ago, with only 70 percent of the labor. In addition, according to Assembly Mag, more than 2.3 million manufacturing jobs created in the next 10 years will go unfilled.
Labor shortages are an ongoing problem for manufacturers, and automation offers a viable solution. According to Boston Consulting Group, manufacturing tasks performed by robots are expected to increase in the U.S. by 30–45 percent from 2015 to 2025, in large part because robots are less expensive and thus more accessible for smaller factories. But labor shortages aren’t the only motivation for automation. Automation technology also helps to increase labor productivity significantly, both by increasing efficiency and by reducing workplace injuries that result in the need to hire and train temporary workers.
Automation and worker safety: a symbiotic relationship
Workplace injuries are a key driver of loss for U.S. businesses, costing more than $1 billion per week and $59 billion annually according to Liberty Mutual’s 2020 Workplace Safety Index. And for the manufacturing industry, the top five injury causes account for almost $5.2 billion (or 63 percent) of injury-related costs. Looking at these top causes, which include handling objects, falls on the same level, being hit by objects, running equipment, and awkward postures, it becomes clear how automation can help improve safety and reduce costs.
With automation technology, employees can work smarter and safer, avoiding many tasks that lead to workplace injury in the first place. For example, collaborative robots, or cobots, can work alongside human workers to help increase efficiency on the factory floor. Workers may also be able to avoid or limit heavy lifting, repetitive tasks, and contact with machinery or harmful materials — top causes of injuries and workers compensation claims and costs.
In addition to creating a safer work environment, adopting automation can benefit workers in other ways:
- By leveraging cobots to help with physically demanding and repetitive work, employees can focus on upskilling to more intellectually challenging jobs, which can lead to higher pay and greater job satisfaction.
- Rather than doing repetitive manual labor, employees can focus on maintaining and reprogramming cobots and managing other automated systems.
- And because cobots aren’t human, they can help improve overall factory safety – they are never sick or tired, and they never forget safety checks.
Three practices for effective automation installation
While the benefits of automation are clear, it can be challenging to determine the best strategies to implement automation effectively at your company. Here are three best practices to guide your process.
1. Focus on the most critical business needs.
Automation is modular, which means you don’t need to implement it across the board. Taking an agile approach and putting automation where it’s most critically needed will help you manage expenses and reduce confusion as you change procedures. If you want to reduce slips and falls, for instance, install sensor technology. To help drive more productivity, consider cobots. When you take this approach, you don’t need as much upfront investment, and you can more closely monitor how automation is impacting your bottom line.
2. Put the right talent in the right place.
Automation is only as great as the workforce maintaining and designing it. Make sure that you have the right talent in the right place by identifying the roles you need to fill and offering training programs to upskill your current employees. To address potential skill gaps, reach out to technical colleges and sponsor training programs to create a job pipeline for graduates interested in working with automation technology.
3. Re-examine your risk-management program.
When you install automation technology, you’ll likely need to re-evaluate your risk-management plan. For example, you may need to explore cyber coverage for your new equipment or increase your coverage limits for property, equipment breakdown, and business interruption, so that if your automation technology is broken or damaged you can easily recover your losses. So that you aren’t introducing new safety risks while eliminating other ones, you should also train employees, including maintenance crews and managers, on how to operate automated technologies properly.
Automation boosts the bottom line.
Beyond individual worker safety, an environment of increased safety due to automation can also boost the bottom line. The overall cost of workplace injuries ranges in the billions of dollars every year, and the American Society of Safety Professionals estimates that the indirect costs of a workplace injury are as much as 20 times greater than direct costs, such as medical bills. Indirect costs include hiring temporary workers, reduction in morale because of the injury, and the administrative costs of returning an employee to work. In today’s uncertain economy, reducing costs while improving employee safety and morale is a win-win.
The use of cobots on manufacturing floors is growing. Learn more about how cobots can help reduce the risk of employee injuries and increase worker efficiency and ways businesses can manage potential risks.
Related insights
This website is general in nature, and is provided as a courtesy to you. Information is accurate to the best of Liberty Mutual’s knowledge, but companies and individuals should not rely on it to prevent and mitigate all risks as an explanation of coverage or benefits under an insurance policy. Consult your professional advisor regarding your particular facts and circumstance. By citing external authorities or linking to other websites, Liberty Mutual is not endorsing them.