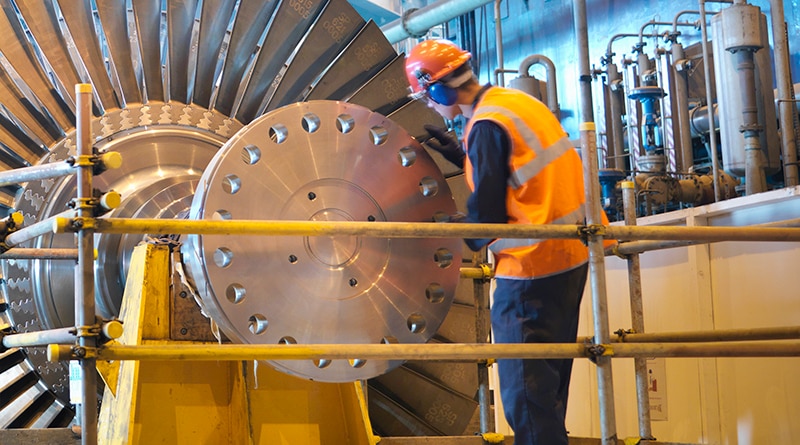
The manufacturing sector is a key driver of the U.S. economy, providing nearly 13 million jobs and generating more than $2 trillion in gross domestic product (GDP) in the third quarter of 2018. Even with this activity, several factors challenge growth. From incorporating technologies like blockchain, co-bots, and “smart facilities” to addressing talent shortages, supply chain disruptions, and intellectual property theft, the manufacturing sector faces a variety of emerging risks.
The Manufacturing Risk Matrix featuring 10 critical risks
The Risk Matrix, produced by the editorial team at Risk & Insurance®, plots critical risks facing the manufacturing industry based on the frequency and severity of each risk.
Product recall
In addition to causing major disruptions to a manufacturer’s supply chain, product recalls can also be very costly. Food-related recalls, including both direct and indirect costs, may amount to as much as $10 billion every year. In addition to covering expenses for executing a recall, manufacturers may also experience lost sales, litigation, regulatory fines, and reputational damage. Technology like blockchain, sensors, and telematics are providing manufacturers with real-time traceability of products so they can more quickly identify and remove defective inventory from the supply chain. In addition, establishing formal quality assurance procedures and taking other proactive steps can help a manufacturer prepare for and survive a product recall.
Blockchain
For manufacturers, blockchain has the potential to add value throughout the supply chain—from track-and-traceability and regulatory compliance to asset maintenance and contracts management. According to a recent report, managing supplier contracts is the most popular blockchain use case for manufacturing organizations. However, there are challenges that come with adopting this emerging technology. For example, regulatory and legal environments are still playing catch up and are open for interpretation. In addition, integrating blockchain with legacy systems requires significant capital investment.
Direct-to-consumer models
Going direct to consumer (DTC) can result in increased efficiency and greater profits by cutting out the middlemen — wholesalers and retailers. It also affords manufacturers more control over the customer experience. But pursuing a DTC strategy may also introduce new risks that middlemen would typically retain. It could bring exposures related to product labeling, handling customers’ credit card data, or the logistics of shipping to residential doorsteps. It could also damage existing relationships with wholesale distributors and retailers that manufacturers may need to rely on in the future.
Skills gap
A 2018 report by Deloitte and the Manufacturing Institute estimates that the current skills gap may leave 2.4 million manufacturing positions unfilled between 2018 and 2028. Many Americans see a lack of stability, growth opportunities, and competitive salaries in the manufacturing industry. At the same time, experienced workers are retiring, and the skill sets needed by manufacturers are shifting due to evolving technologies. To bridge the skills gap, manufacturers should think proactively. For example, by partnering with local governments and secondary schools to engage potential applicants earlier through apprenticeship programs or introducing co-bots or wearable technology to help boost productivity.
Tariffs
Recently imposed tariff increases on steel and aluminum imports from several countries are increasing raw material costs for many manufacturers that source from international suppliers. As a result, many companies are considering new suppliers from regions not impacted by tariffs. While diversifying supplier relationships is one way to address increasing costs, product defect liability and supply chain disruption risks could outweigh the benefits.
Intellectual property protection
Theft of intellectual property (IP), including patents, trade secrets, trademarks, and copyrights, costs manufacturers and other businesses billions of dollars every year. A 2017 investigation by the U.S. Trade Representative concluded that annual cost of IP theft to the U.S economy is between $225 billion and $600 billion. Expanding operations overseas can create greater opportunity for IP infringement and theft as supply chains and networks grow. Regulatory, legal, and trade protections may also be absent or less stringent in other countries. For a manufacturer that has invested considerable time and resources developing products, processes, or ideas, implementing an IP risk management strategy is critical for long-term success.
Global supply chains
A variety of potential disruptions, from grounded flights and natural disasters to cargo theft and quality control issues, can impact the flow of goods through a supply chain. If a supplier doesn’t make a delivery, operations may grind to a halt. If a product component is defective, a business could face legal or regulatory violations. Manufacturers will likely also face lost sales and damaged reputations. In today’s global economy, companies that proactively plan how to mitigate supply chain disruptions will be better positioned to deliver their products on time and on budget.
"Smart" facilities
Manufacturers are expected to spend close to $267 billion on Internet of Things (IOT) by 2020 to improve productivity by increasing automation, improving equipment monitoring, and better connecting systems. But as manufacturers incorporate IOT and other technologies into operations, they also become more vulnerable to cyber-security threats that could put their physical assets, intellectual property, and more at risk. Taking steps to prioritize cyber-security and insurance protections can help safeguard your smart facility from hackers and minimize the risk of downtime and lost profits.
Co-bots
More than 3 million industrial robots will be in use in factories around the world by 2020, according to the International Federation of Robotics. Collaborative robots, or co-bots, which work alongside workers, can help bridge talent shortfalls and improve productivity in the manufacturing industry. As manufactures incorporate co-bots into their operations, they also need to address potential risks. For example, manufacturers could be held liable for product defects, personal injury, or property damage resulting from co-bot failures or malfunctions.
3D printing
Additive manufacturing, or 3D printing, can help manufacturing operations boost production and reduce costs, but this new technology may also introduce risks related to counterfeiting, product liability, professional liability, and more. Criminals may create and sell counterfeit, lower-quality versions of a manufacturer’s products, which could result in false product liability claims. The separation between product designer and producer also blurs, raising questions about which party is responsible for product defects.
The Risk Matrix is featured with the permission of Risk & Insurance®. The Risk Matrix is produced by the Risk & Insurance editorial team.
This website is general in nature, and is provided as a courtesy to you. Information is accurate to the best of Liberty Mutual’s knowledge, but companies and individuals should not rely on it to prevent and mitigate all risks as an explanation of coverage or benefits under an insurance policy. Consult your professional advisor regarding your particular facts and circumstance. By citing external authorities or linking to other websites, Liberty Mutual is not endorsing them.