

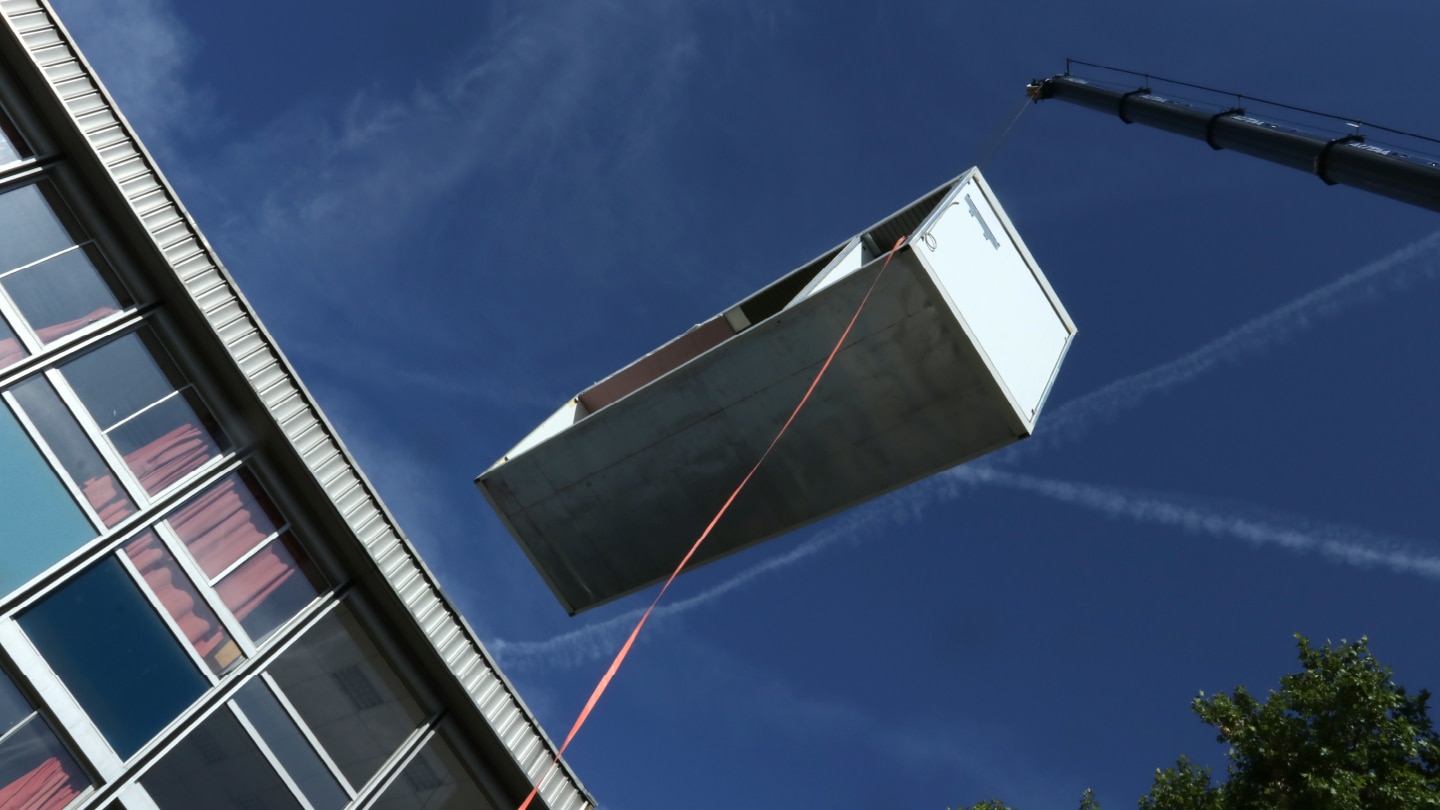
Modular construction is on the rise. Today many buildings are being manufactured in pieces to create dorms, hotels, apartments, and even new schools. The buildings are being built in an assembly-line manner, with individuals completing the same task repeatedly. These pieces are built off site, shipped to the job site, and installed to create a quality building with architectural features.
One recent example is a CalTrans apartment complex which was built to provide temporary housing for snowplow drivers during the winter months. The individual components were manufactured in North Dakota, numbered, placed in a rail car, and shipped to Sacramento Valley where they were installed and placed in a staging yard. As construction started, the contractors would pull the numbered piece out from the staging yard, truck it to the job site, and install each piece. The pieces, all installed in North Dakota, contained most elements of an apartment building — cabinetry, Romex for electrical, drywall, shower tub combos, tile flooring, and granite countertop. The quality was everything you would expect from traditional construction, except these buildings were being built in pieces and fit together like Legos.
“Research suggests this particular type of construction will continue to grow by nearly 6 percent between 2020 and 2025. And why not? It is fast, environmentally friendly, safe, and cost-effective.”
Another example comes from Hickory Construction, a company that built a six-story apartment building with 77 apartments in 10 days after the site and underground work was completed. The total lead time was less than 12 months, which resulted in saved time and costs.
Research suggests this particular type of construction will continue to grow by nearly 6 percent between 2020 and 2025. And why not? It is fast, environmentally friendly, safe, and cost-effective.
Surety considerations for modular projects
As with any traditional construction project, when underwriting a performance and payment bond for a modular project, sureties must take into consideration several factors:
1. Design elements
Piecing together a large apartment community requires more decisions to be made in the design and engineering stages. This requires architects, engineers, and contractors to be familiar with modular construction. Any failure within the design stage may trigger delays. If the contractor is responsible for designing the project, these delays can cause margins to suffer, or worse, eat into working capital and net worth. This impacts a contractor’s balance sheet, which is integral to surety underwriting decisions.
2. Supplier risk
Once the contract is signed, the manufacturer of the modular building will become a contractor’s main partner for the duration of the project. Key questions the contractor should ask include:
- Can the manufacturer meet the timeline?
- What happens if the manufacturer cannot meet the schedule or ceases business operations? Can the contractor replace the manufacturer, or will the contractor need to go back to the design/engineering stage with a new manufacturer?
Surety underwriters are very interested in how thoroughly the contractor prequalified the modular builder (i.e., manufacturer). The modular builder will have a sizeable portion of the contract and will be a critical path subcontractor for the duration of the project. Surety underwriters may encourage contractors to require a performance bond from the modular builder or want to know how the contractor prequalified the modular sub.
3. Transportation
In the CalTrans example, the modular buildings were manufactured in North Dakota. The pieces were placed on a rail car and transported 1,900+ miles from North Dakota, across Montana, and down through Oregon before arriving at the final destination in the Sacramento Valley. Contractors should take into consideration distance and evaluate the type of delays and damages that may occur during transport. When utilizing just-in-time delivery, contractors should understand the risks. Shipping delays and damages can result in other costs, trigger liquidated damages, or actual damages clauses. It is important that contractors review contract language pertaining to damage delay clauses to determine the best method of material delivery to minimize risk and complete a profitable project. Bottom line: surety underwriters want to make sure the contractor is comfortable with the timeline and ensure they have taken all these factors into consideration.
4. Construction defects
The fast pace of modular projects is great for reducing project construction time, as evidenced by the Hickory example, where the company was able to build the foundation at the same time as the modular work was being done. Automation can provide quality modular builds with the right equipment and employees. Conversely, modular build quality can suffer with the wrong employees or equipment, devastatingly requiring repairs for multiple buildings once they are received at the project site.
“Regardless of the manner of completion, contractors should ensure they have the right labor in place, understand local legislation and always keep quality at the forefront.”
If the units are not constructed properly and repairs are not made, the risk of construction defects increases and can impact the quality and safety of the building. Contractors and manufacturers that participate in modular construction should have a detailed quality assurance program to ensure the work done before installation is of the highest quality. Poor build quality can require rework, causing delays and unexpected costs to occur.
To help with the underwriting process, modular contractors should be able to answer questions regarding their experience with the modular building supplier and what they have done to prequalify the supplier.
5. State and local building codes
Modular building contractors must be aware of varying state and local building codes and adhere to those codes. For example, some municipalities allow modular buildings to be delivered with their walls closed, while others prevent walls from being closed until a local building inspector has had the opportunity to inspect the electrical or mechanical equipment. No matter how they are constructed, all projects must meet federal, state, and local codes. Surety underwriters ensure contractors are knowledgeable about these codes. If a contractor is moving into a new territory, surety underwriters will remind contractors that building code knowledge is key.
6. Prevailing wage issues
Contractors must be knowledgeable about prevailing wage issues. In the CalTrans example, a project labor agreement or a prevailing wage payment was a requirement on the project. Under California law, contractors are responsible for unpaid prevailing wages and unpaid penalties, even if a subcontractor or supplier completed the work. The contractor must assess its contractual obligation to determine if a modular builder will fall under a subcontractor, manufacturer, or supplier classification. This determination could mean the modular builder must pay prevailing wage.
7. Labor
The difference in complexity between a single-story modular building and a high-rise or mixed-use development modular building can be exponential. If a mixed-use high-rise building is off by a quarter of an inch, it can make the next floor construction more difficult, eventually leading to structural flaws in the building. Construction labor availability continues to be a challenge, and the lack of experience assembling these buildings can make it more difficult for contractors looking to enter the modular building market. Contractors can turn to construction assembly professionals, who are becoming more and more proficient in modular construction. Surety underwriters will look to ensure the right labor is in place so that the project is completed within its parameters.
In short: labor, laws, and quality
The way a surety underwrites a modular construction project is not all that different from a traditional construction project. Regardless of the manner of completion, contractors should ensure they have the right labor in place, understand local legislation, and always keep quality at the forefront.
To learn more about contract surety, visit us online or contact your independent agent.
Featured insights
This website is general in nature, and is provided as a courtesy to you. Information is accurate to the best of Liberty Mutual’s knowledge, but companies and individuals should not rely on it to prevent and mitigate all risks as an explanation of coverage or benefits under an insurance policy. Consult your professional advisor regarding your particular facts and circumstance. By citing external authorities or linking to other websites, Liberty Mutual is not endorsing them.